FDT-01 Dart Impact Tester Features
- Color touch screen interface, convenient and intuitive operation
- Dual test mode, automatic judgment of test status
- Electromagnetic suspension drop hammer, automatic release to reduce errors
- Pneumatic clamping, dual start mode, flexible operation
- Built-in observation light, improve test visibility
- Professional software support, multi-unit and graphic display
- Built-in printer and RS232 interface, convenient data transmission
Impact Testing Machine
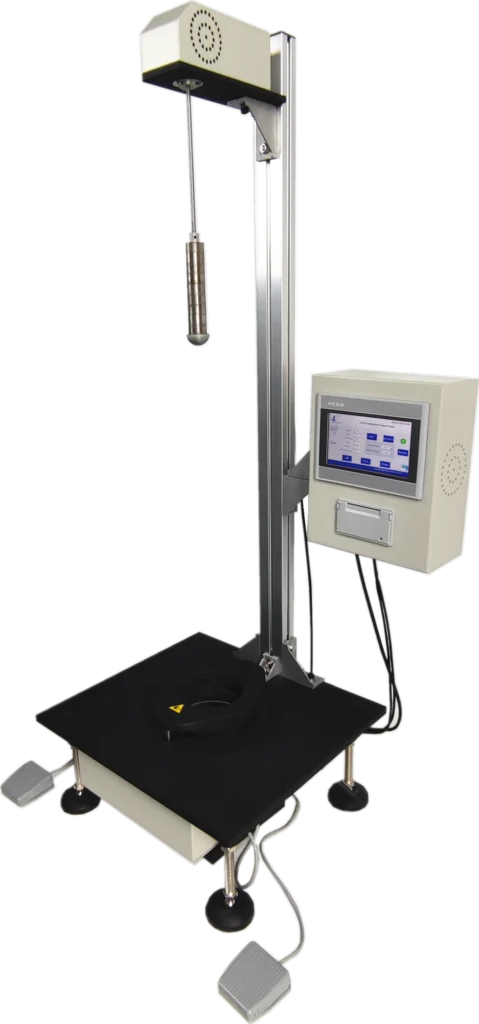
Impact Testing Equipment
What is Impact Resistance?
Impact resistance refers to a material's ability to withstand cracking, breaking, or deformation when subjected to sudden external forces, such as impacts or drops. It is a critical property that directly influences the material’s safety, durability, and reliability in real-world applications.
Dart Drop Testing Standards
ASTM D1709, ISO 7765-1-1988, JIS K7124-1, GB/T 9639.1-2008
Dart Impact Testing Principle
Before starting the test, select the test method and estimate the initial impact mass and increment Δm. Once the test begins, if the first specimen fails (breaks), reduce the mass of the falling dart by Δm; if it does not fail, increase the mass by Δm. Continue testing according to this rule. After testing 20 specimens, count the number of failed specimens N:
- If N = 10, the test is complete;
- If N < 10, continue testing until the number of failed specimens reaches 10;
- If N > 10, continue testing until the number of non-failed specimens reaches 10.
Finally, the tester will automatically calculate the test result according to specific formulas.
Applications
Industry Category | Typical Materials | Application | Test Standards |
Food packaging | PE, PP, BOPP, PET, composite film | Snack bags, frozen food bags, vacuum packaging film | ASTM D1709, ISO 7765-1 |
Pharmaceutical packaging | PVC, PVDC, aluminum-plastic composite film, multi-layer co-extrusion film | Infusion bags, tablet blister packaging, syringe bag film | ISO 7765-1 |
Medical device packaging | Medical grade polyethylene film, sterile barrier system film | Sterile dressing packaging, medical device soft packaging bags | ASTM D1709, ISO 11607 |
Daily chemical product packaging | PE, PET, nylon composite film | Shampoo refill packs, cosmetic soft bags, liquid detergent bags | ASTM D1709 |
Electronic product packaging | Conductive PE film, antistatic film, cushioning air film | IC component packaging film, antistatic gasket packaging | ISO 7765-1 |
Technical Specifications
Specifications | FDT-01 Falling Dart Impact Tester |
Test Method | A or Method B (optional) |
Test Range | Method A: 50~2000 g |
Method B: 300~2000 g | |
Accuracy | 0.1 g (0.1J) |
Clamp | Pneumatic Clamp |
Pressure of Gas Supply | 0.6 MPa (outside of supply scope) |
Port of Gas Supply | Φ8 mm PU Tubing |
Specimen Size | > 150 mm x 150 mm |
Power Supply | AC 110~220V 50Hz |
Instrument Dimension | Method A: 500 mm (L) x 450 mm (W) x 1200 mm (H) |
Method B: 500 mm (L) x 450 mm (W) x 2200mm (H) |
Ensure the impact resistance of packaging materials
The core function of the dart impact tester is to determine the critical point of rupture of plastic film or sheet under impact load. This is extremely important for the packaging industry.
- Transportation safety: Packaging must resist impacts from drops during transport and handling.
- Shelf performance:Accidental impacts during shelving or stacking may damage packaging and affect sales.
- User experience: Damaged packaging upon receipt harms brand image.
impact resistance testing
Comply with international standards and improve market access
Dart impact testing is usually carried out according to international standards such as ASTM D1709 and ISO 7765-1, which are quality requirements that many export products must meet.
- ASTM D1709: Method A and Method B are used to determine the resistance of films to free-fall impact respectively.
- ISO 7765-1: Applicable to free-fall impact testing of plastic films or sheets.
impact resistance testing
An important tool for quality control
During the production process, the dart tester is a key quality control device.
- Raw material screening: Test results reveal impact strength differences among suppliers, aiding in selecting quality materials.
- Process optimization: Adjust temperature, speed, and cooling during production based on test results.
- Batch consistency detection: Ensure consistent impact resistance across batches to maintain product quality.
impact resistance testing
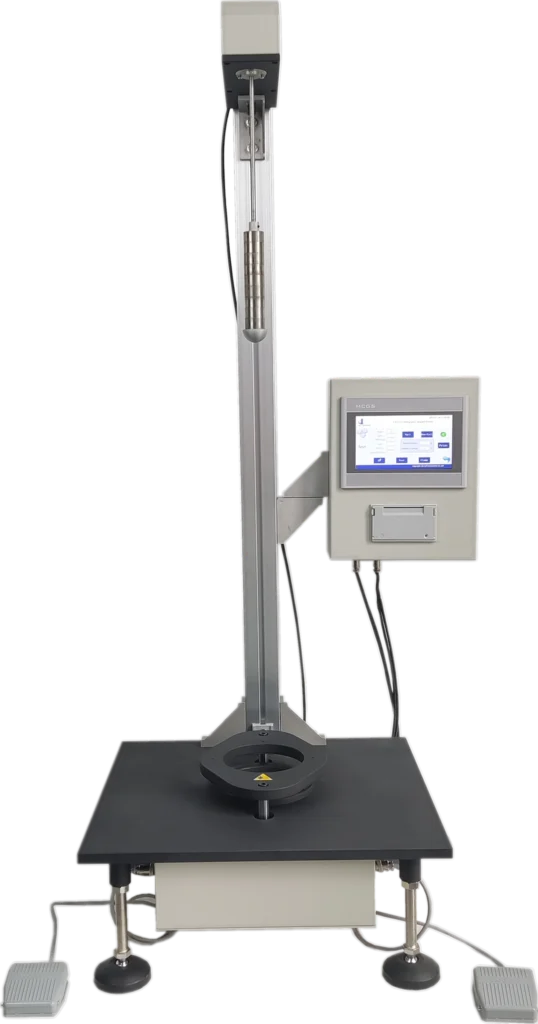
free falling dart impact tester
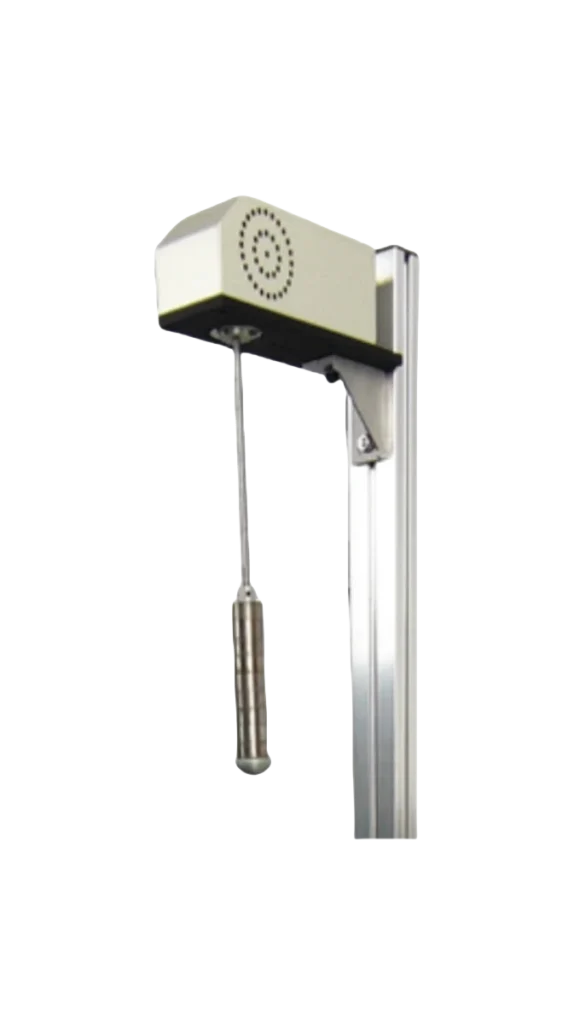
free falling dart impact tester
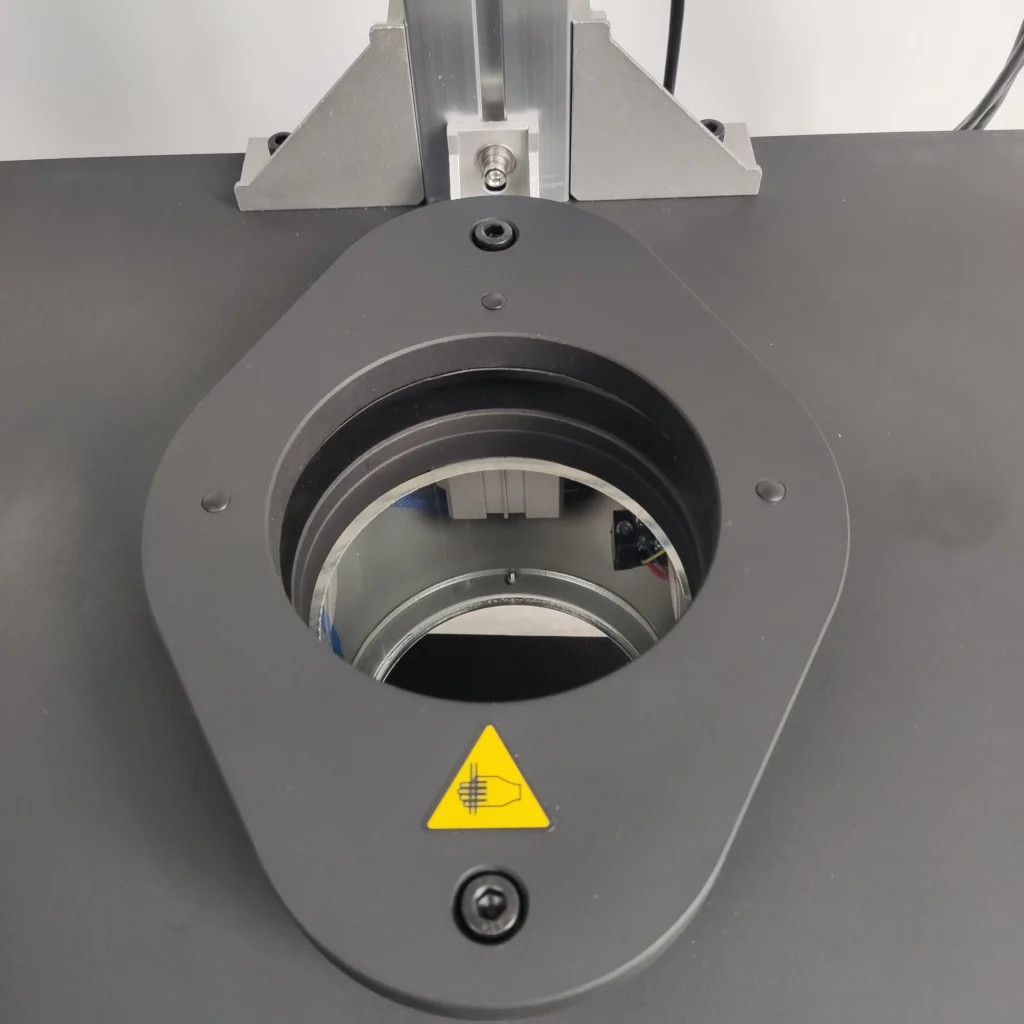
free falling dart impact tester
Conclusion
dart impact test
The dart impact tester is the core instrument for evaluating the impact resistance of films. It plays a vital role in production quality control, material R&D verification, standard compliance testing, and packaging safety assessment. It not only ensures product integrity throughout the supply chain, but also helps companies improve product quality and consolidate brand reputation in a highly competitive market.
Cell Instruments Advantages
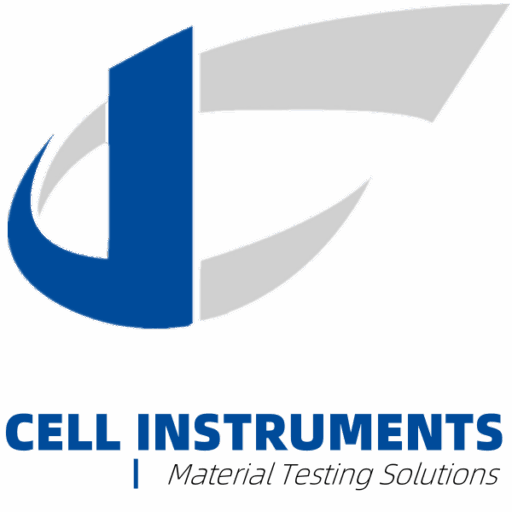
Professional manufacturer background
With many years of R&D and production experience, we focus on packaging, medicine, food, and electronics. We have a strong R&D team and modern manufacturing system to ensure leading product quality and technical level.
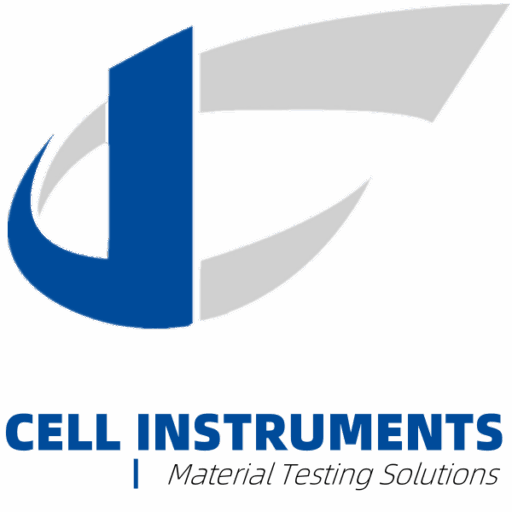
Strong custom development capabilities
With deep technical accumulation, we provide tailor-made solutions, including function adjustment, software customization, and automation transformation, to flexibly respond to various testing needs and improve testing efficiency.
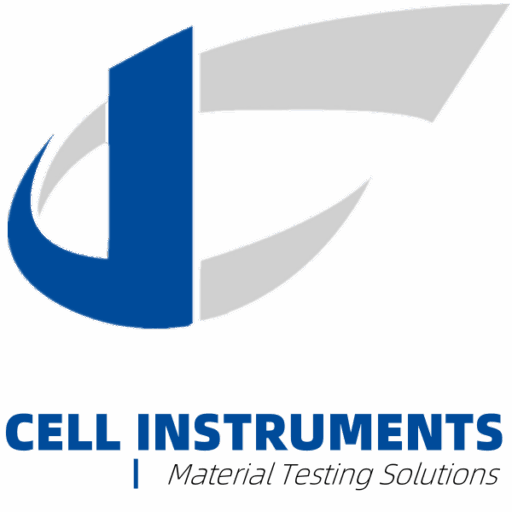
Complete after-sales service system
With a technical support and after-sales service network covering the national and overseas markets, we provide full-service services such as operation training and remote diagnosis to ensure that customers are worry-free and minimize downtime.
Frequently Asked Questions
1. What is the primary purpose of the Dart Impact Tester?
The Dart Impact Tester measures the impact resistance of plastic films, which is crucial for ensuring the durability and performance of packaging materials under stress.
2. How does the Dart Impact Tester comply with ASTM D1709 and ISO 7765-1?
Our Dart Impact Tester is designed to meet the specifications and requirements outlined in ASTM D1709 and ISO 7765-1, ensuring accurate and reliable test results.
3.How does this differ from pendulum impact testers?
Falling Dart Testers are designed for vertical free-fall impact on flexible materials like films,
while pendulum impact testers (e.g., Charpy or Izod) are used for rigid materials like plastic sheets to assess impact toughness.
4. Can the Dart Impact Tester be customized for specific testing needs?
Yes, Cell Instruments offers customization options to tailor the Dart Impact Tester to specific testing requirements, enhancing its functionality and relevance for different applications.